|
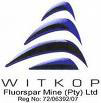
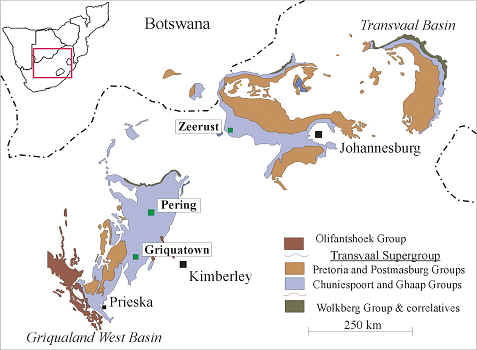
Geological sketch map illustrating the distribution of carbonate-hosted
Zn-Pb and F deposits
in the dolostones of the Transvaal Supergroup.
WITKOP
FLUORSPAR MINE EXPANSION
At the end of June an R11 million (US$1.8 million) plant upgrade at Sallies
Witkop fluorspar mine located just south of Zeerust in South Africa was
near completion and this will see its production increase from 100,000
tonnes to 180,000 tonnes a year.
Sallies, a Johannesburg Stock Exchange listed company for 100 years, with
the Witkop fluorspar mine as its main asset, ran into difficulties during
2003. This was attributed to a combination of factors including an inefficient
head office management structure coupled with high head office costs.
The operation, which employs 200 people, suffered from plant breakdowns
due to poor maintenance as a result of a lack of funding and this led
to fluctuating plant efficiencies. This was exacerbated by irregular power
supply and the end result was a varying product quality and a decrease
in acid grade fluorspar volumes. This together with the strengthening
rand and deterioration in head grade saw the operation making losses.
As a result the turn around specialist FMR was appointed in February 2003,
for three years, to implement a programme to return the company and the
mine to profitability. The key of the turn around strategy involves the
mine increasing output at a lower unit cost. At the start of 2004 Sallies
raised R36 million (US$6.5 million) through a rights offer and some of
this funding was allocated to expand and upgrade the Witkop plant.
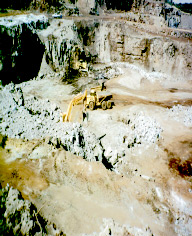
One of the Wintershoek open pits at Witkop.
Witkop is
a low grade fluorspar operation that was selectively mined by Phelps Dodge,
its previous owner until 1999, but with these areas having been depleted
the mine now has to mine ore at an average lower grade. Sallies plans
to operate the mine at a head grade of 12% using a more steady resource
management basis than was previously done. To offset these lower grades,
a new ball mill, Number 3 mill, was commissioned in April, and Number
4 mill as well as the Number 6 regrind mill were commissioned in June
2004 to increase tonnage throughput by the Witkop plant.

A blast at the Witkop fluorspar mine
The operation
has two open pit ore bodies, Wintershoek, mined from about three open
pits, and Buffelshoek. A blend from the two ore bodies is optimal for
the plant throughput and recoveries. Wintershoek has proven reserves of
17.8 million tonnes at a grade of 14.3% CaF2 (fluorspar), while Buffelshoek
has a reserve of 9.5 million tonnes at a grade of 18.6% CaF2. The Wintershoek
ore body is the one currently being predominantly mined and at a production
rate of 180,000 tonnes a year it will have a life of mine of another eight
years.
The Witkop operation involves drilling, blasting, loading and haulage
using Cat and Bell equipment, followed by the blending of the ore from
the two different ore bodies, and a crushing stage involved primary, secondary
and tertiary crushing. This is followed by milling and classification,
a pre-float and thickening stage, and a rougher stage where the concentration
of CaF2 is upgraded to 30%. There are several cleaner stages which increasingly
upgrade the percentage of CaF2 content. The operation also makes use of
a regrind mills and the final product contains 97% CaF2 with only 2% manganese
and copper and 1% silica and iron. After filtration to dry it, the product
is transported via the Lucerne station where it is loaded on 54 tonne
rail cars. Fluorspar for the local market is sold in 25 kg bags, or in
bulk.
THE FLUORSPAR
MARKET
The mine produces both acid grade (greater than 97% purity) and metallurgical
grade (less than 97% purity) fluorspar. Metallurgical grade fluorspar
is used as a fluxing agent in the manufacture of steel, stainless steel,
cement, ceramics and glass, and the mine supplies customers such as Iscor,
PPC, Highveld Steel and Consol Glass. The acid grade fluorspar is used
in combination with sulphuric acid to form hydrogen fluoride (HF), and
with sulphuric acid and aluminium hydrate to form aluminium fluoride (AlF3).
Hydrogen fluoride is further processed into refrigerant gases, HCFC
which is an interim replacement for ozone unfriendly CFCs and HFC,
which will phase out HCFC over time, and which coincidently uses twice
as much acid grade fluorspar. The market for aluminium fluoride is also
a promising one in that it is further processed into downstream aluminium
products, one of the faster growing world markets.
Like many other commodities fluorspar benefits from Chinas ongoing
rapid modernisation. The production of fluorspar is dominated by China,
which produced 54% of world output in 2002, followed by Mexico at 14%,
while Europe and Russia account for another 13%. In 2000 Chinese exports
were two million tonnes of fluorspar, but this dropped to 750,000 tonnes
in 2003 as the countrys internal consumption increased. It is estimated
that Chinese exports will decrease further in 2004 to 420,000 tonnes.
Sallies chief executive Lindsay Robertson predicts that by 2010 China
will not be exporting fluorspar, which leaves a gap to fill and he says
that Sallies wants to be one of the companies that fills it.
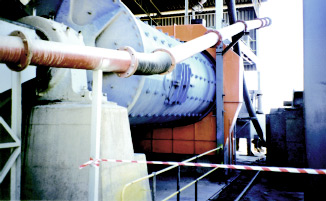
One
of the new mills installed at Witkop to increase throughput.
South Africa accounts for about 5% of world fluorspar production, with
the countrys main producers being Witkop and the Vergenoeg operation,
owned by Metorex, which produces about 100,000 tonnes a year and which
is also looking at a possible increase in production. There is also the
Buffalo fluorspar recycling operation that is capable of producing some
10,000 tonnes a year and this could increase with investment in plant.
Witkops production averaged 100,000 tonnes a year between 1998 and
2003, and once the expansion/upgrade is complete, the operation that works
24 hours a day every day of the year, will produce 550 t/day of fluorspar
and on good days it could up this to 600 t/day. At the end of July it
will be producing at a level of least 450 t/day.
Although South Africa is a relatively small producer, a mine such
as Witkop has advantages in terms of the quality of product compared with
others that makes the fluorspar it produces a desirable product,
Robertson says. For example, Mexicos fluorspar is high in
arsenic content, an undesirable contaminant, whereas the South African
fluorspar can trade at a premium because of an almost zero arsenic content.
Another example is that in comparison to Kenyas fluorspar, which
is high in P2O5 and is unsuited for aluminium production, South African
fluorspar is low in P2O5.
One of the problems faced by Witkop is that with production running as
low as 60,000 tonnes a year at one stage before its turnaround began,
it has fallen behind on a five-year contract with its main customer Honeywell
in the US. It is a five-year contract begun in 2001 that requires the
mine to provide 85,000 tonnes a year of acid grade fluorspar. In June
2004 this contract was six months behind schedule, with some 170,000 tonnes
still to be delivered before the end of 2005, and the mines increased
output will go towards meeting this obligation. Robertson says that unfortunately
the mine negotiated this contract as one where Honeywell dictates the
price paid for the fluorspar based on the average price it receives from
its other suppliers, and this has seen Honeywell paying US$100/t compared
with a spot price of US$135/t. The spot market for fluorspar is small,
mainly a result of shortfalls due to suppliers unable to meet their contractual
tonnages, as was the case with Sallies in its recent past. Robertson says
that any future contracts will be negotiated differently, and that even
under the current contract the price paid by Honeywell will go up to a
minimum of US$110/tonne, with fluorspar prices having increased. In addition
to meeting these contractual obligations, Sallies has arranged to supply
four different customers in Europe, the most important being Bayer, with
prices being paid not less than US$130/t. In total the company expects
to get an average sales price per tonne of US$120 for its next financial
year. Robertson says that the company is looking at prices better than
US$140/t in 2005.
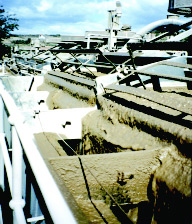
Flotation circuit at the Witkop plant.
These prices
will make the mine profitable at a rand/dollar price of 6.5:1, but the
company has a contingency plan should the rand remain at a higher level.
This involves the recycling of tailings, where a drilling programme has
been completed and a 50 t/h pilot plant was running at the end of June
2004. A full tailings recycling project could be underway by the end of
March 2005 and one of the tailings dumps containing up to 6% fluorspar,
Dump 1, has sufficient material to provide the plant with 500 tonnes a
day for ten months. In all Witkop has an estimated 45 million tonnes of
tailings material that could be considered for recycling. The pilot plant
produces a slurry of 20% CaF2, which is then added into the processing
circuit. It is not envisaged that the mine would cease operating altogether
and rely completely on dump tailings processing, even under strong rand
conditions.
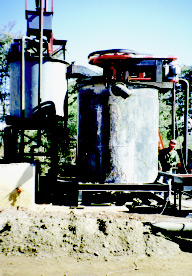
The pilot plant for the recovery of tailings at Witkop.
THE TURNAROUND
The initial
turnaround strategy implemented by FRM involved a corporate restructure
that saw Sallies Johannesburg head-office closed down. Negotiations
with Eskom also saw the consistency of power supply restored, and this
together with the companys focus on maintenance has improved plant
availability. The new management also visited major customers, such as
Honeywell, whose plant is suited to the Witkop product, to cement the
continuing long-term relationship. The aim is to supply 50% of the bulk
of the mines output to Honeywell, and the other 50% to Europe and
the Far East. Some 10,000 to 20,000 tonnes may be reserved to take advantage
of the small spot market.
FRM has decreased the mining cost per tonne from R25/t (US$4/t) to R15/t
(US$2.50/t). This was done by converting from contractor to owner mining,
which began in October 2003, thanks to financing from WesBank that enabled
the purchase of new equipment. That means the total processing cost of
the final product is about R200 250/t (US$33 41/t), to which
is added rail costs from Zeerust to Durban and Durban Bulk Terminal costs
that together total about R300/t (US$50/t). The FOB break even cost for
the Witkop mine is thus about or below R700/t (US$115/t).
The Witkop property covers 8,000 ha, of which 312 ha is used for mining,
and the operation will need to determine where it will mine in the future,
and make a decision on portions of the property which do not contain any
such resources. Sallies is also disposing of its East Rand mineral and
property rights to focus on its Witkop fluorspar operation.
Texte issu
de :
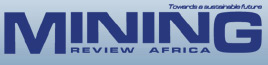
http://www.miningreview.com/archive/mra_4_2004/42_1.php
http://www.miningweekly.co.za/article.php?a_id=99355
Fluorspar
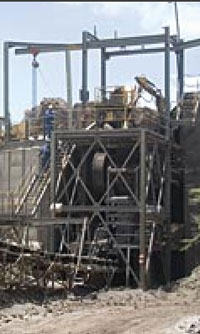
Related articles
Some workers down tools at Sallies' Witkop mine
Fluorspar producer Sallies said on Thursday that its wage payroll workers
at the Witkop mine have downed tools on Wednesday night over pay demands.
Witkop miners return to work
The 200 workers that had been locked out at fluorspar miner Sallies? Witkop
mine, near Zeerust, last week were back at work, the company said on...
Witkop Fluorspar mine, North West Province
Sallies workers end two-day strike
Fluorspar miner renews efforts to end strike
By: Carla Fernandes
Published: 19 Jan 07 - 0:00
Name:
Witkop Fluorspar Mine.
Location:
Witkop mine is located 18 km south of Zeerust in the Marico district,
North West province.
Brief
history: Sallies was incorporated in 1903 as the South African Land and
Exploration Mining Company Limited and has been listed since 1904 in the
mining sector of what is now JSE Limited. On July 1, 1999, the company
acquired a 100% interest in Witkop Fluorspar Mine (Proprietary) Limited
and its wholly-owned subsidiary, Marico Fluorspar (Proprietary) Limited
for R80-million. Following its acquisition of the Witkop mine in the North
West province of South Africa in 1999, the company changed its name to
Sallies Limited.
Brief
description: Witkop has an estimated mine life of 12 to 15 years and employs
250 people.
Products:
Fluorspar.
Mining
method: Opencast.
Reserves:
Total proven reserves as at June 30, 2006, are 26,3-million tons.
Resources:
Unstated.
Geology:
The Witkop fluorspar mineral deposit lies within the Marico Fluorspar
Field, an area of expansive outcropping and subcropping of low- to medium-grade
fluorspar in dolomite. The bulk of the fluorspar mineralisation occurs
as a number of discontinuous zones in the Frisco Formation of the Malmani
Subgroup of the Transvaal Sequence. The predominant host rock for most
of the ore is a grey, medium-grained, sparry dolomite.
Major infrastructure and equipment: Spread over nearly 7 000 ha of surface
rights, with new-order mining rights, Witkop mine uses a fleet of Bell
30-t ADTs and Bell excavators with Komatsu loaders.
Prospects: The mine is engaged in a project to recycle some of its tailing
dams in order to significantly increase its mine life. Further exploration
drilling may be undertaken to increase reserves.
Controlling company: Sallies Ltd (100%).
Contact
person: Helen McKane, investor and media relations.
Unique features: Use of the lowest grade fluorspar deposit in the world.
Contact
details:
Sallies Ltd.
Tel: +27 18 642 8440 Fax: +27 18 642 8426 Website: www. sallies.co.za

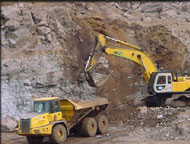
WITKOP
FLUORSPAR MINE
Witkop Fluorspar Mine, an opencast fluorspar mine is situated near Zeerust
in Northwest Province.
The opencast mining and rehabilitation contract was executed from 2001
to 2004.
|